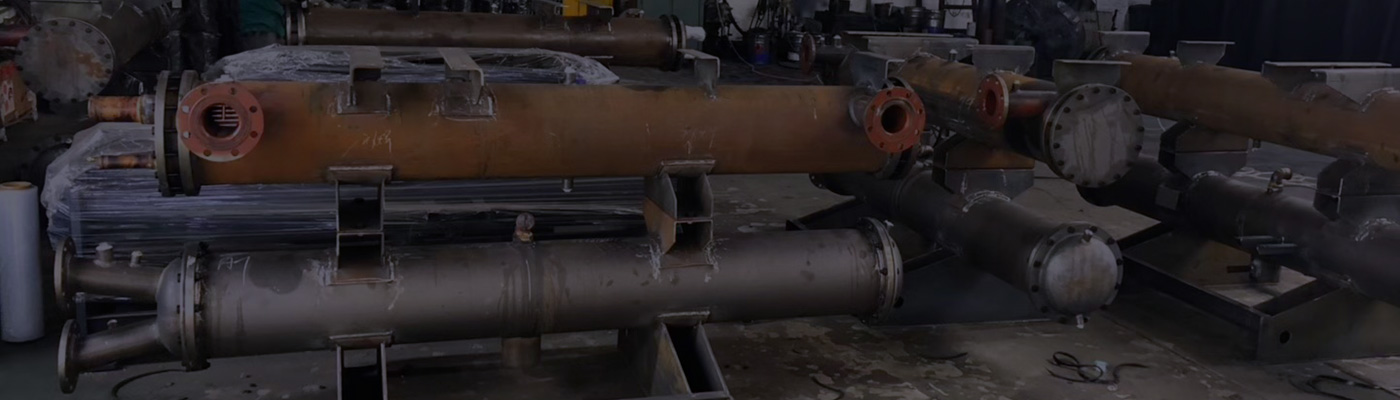
高爐沖渣水直接換熱回收余熱技術(shù)相關(guān)介紹
高爐煉鐵熔渣經(jīng)水淬后產(chǎn)生大量60℃-90℃的沖渣水,其中含有大量懸浮固體顆粒和纖維。目前,我國高爐沖渣水余熱主要采用過濾直接供暖及過濾換熱供暖方式進行利用,但存在容易在管道或換熱設(shè)備內(nèi)發(fā)生淤積堵塞、過濾反沖頻繁取熱量少、產(chǎn)生次生污染等問題,無法長時間使用,因此多年來沖渣水余熱未得到全面有效利用。按照我國鋼鐵生產(chǎn)產(chǎn)量8億t,按350kg渣比計算,由沖渣水帶走的高爐渣的物理熱量約占煉鐵能耗的8%左右,能源浪費巨大。目前該技術(shù)可實現(xiàn)節(jié)能量4萬tce/a,CO2減排約11萬t/a。
技術(shù)內(nèi)容
1.技術(shù)原理
高爐煉鐵沖渣水含有大量60℃-90℃低品位熱量,該技術(shù)采用專用沖渣水換熱器,無需過濾直接進入換熱器與采暖水換熱,加熱采暖水,用于采暖或發(fā)電,從而減少燃煤消耗并減少污染物的排放,達到節(jié)能減排的目的。冷卻后的沖渣水繼續(xù)循環(huán)沖渣,對于帶有冷卻塔的因巴等沖渣工藝,可以關(guān)閉冷卻塔進一步節(jié)約電能消耗;而對于沒有冷卻塔的沖渣工藝,沖渣水降溫后減少了沖渣水蒸發(fā)量,進一步減少水消耗。采用該技術(shù),無需過濾,工藝流程短,運行及維護成本低,取熱過程僅僅取走渣水熱量,不影響高爐正常運行,無次生污染,整體運行可靠,適宜于長周期運行。
2.關(guān)鍵技術(shù)
(1)直接換熱技術(shù)。開發(fā)了專用沖渣水換熱器,解決了纖維鉤掛堵塞和顆粒物淤積堵塞問題,沖渣水無需過濾即可直接進入換熱器與采暖水進行換熱。
(2)抗磨損技術(shù)。沖渣水含有大量固體顆粒物,不僅容易淤積堵塞,而且極易磨損,該技術(shù)通過板型、材質(zhì)、結(jié)構(gòu)、流速等方面的控制解決了磨損問題。
(3)自動運行控制技術(shù)。根據(jù)高爐規(guī)模和沖渣工藝的不同特點,研發(fā)了系列工藝流程與之配套,大型高爐兩側(cè)沖渣的切換技術(shù)以及可靠的直接換熱技術(shù)保證了自動運行的可實施性。
3.工藝流程
高爐容積不同,沖渣工藝不同,以底濾法為例,其工藝流程如圖1所示。由高爐沖渣水泵出口管道處設(shè)置閥組提取沖渣水,取出的沖渣水流經(jīng)沖渣水換熱器取熱降溫后引回原管路繼續(xù)沖渣;采暖水回水流經(jīng)沖渣水換熱器加熱升溫后,供采暖;系統(tǒng)安裝自動控制包含PLC控制系統(tǒng)及溫度、壓力、熱量計量等控制系統(tǒng)。
主要技術(shù)指標
1. 100%全水量取熱,回收熱量大,年產(chǎn)噸鐵可配置采暖面積0.4 m2-0.6m2,節(jié)能5kgce-7.5kgce,節(jié)水40kg-57kg;
2.直接換熱技術(shù),無需過濾、不堵塞,可實現(xiàn)一個采暖季連續(xù)不停車運轉(zhuǎn);
3.大型高爐的因巴等沖渣工藝,冷端溫差小于5℃,可將沖渣水由85℃降至55℃以下;小型高爐的底濾等沖渣工藝,熱端溫差小于2℃,可將采暖水加熱至65℃以上;
4.沖渣水換熱器技術(shù)指標:
單臺最大換熱器面積 1200m2;
單臺最大換熱負荷 1.7×107kcal/h;
單臺最大沖渣水處理量 1400m3/h(底濾法)、500m3/h(因巴法);
換熱器單平米供暖面積 175 m2-500m2。
技術(shù)鑒定、獲獎情況及應(yīng)用現(xiàn)狀
該技術(shù)共獲得國家專利9項,其中2項發(fā)明專利。目前,已在北方20座高爐的沖渣水余熱回收項目中推廣實施,用于城市供暖,其中19座煉鐵高爐,1座銅冶煉高爐,供暖面積累計達1100萬m2,取得良好的經(jīng)濟和社會效益。
推廣前景及節(jié)能減排潛力
隨著高爐沖渣水直接換熱余熱回收技術(shù)的成熟,在有集中供暖需求的北方將得到進一步發(fā)展應(yīng)用。預(yù)計未來5年,該技術(shù)的推廣比例可達40%,項目總投入26億元,可形成的年節(jié)能能力為143萬tce,年碳減排能力為378萬tCO2。
相關(guān)閱讀